
The stiffness of the adjacent members or defined support conditions is thus taken into account directly. This is not a separate calculation by "separating" the individual members, but a calculation on the entire model. The add-on extends the calculation of member elements by the 7th degree of freedom. Stability Failure Due to Lateral-Torsional BucklingĮquivalent Stress Analysis with Internal Forces from Torsional Warpingīoundary Conditions for Calculation with Torsional Warping This distance is too far apart to be considered lacing.Defining End Plate at Member Start and End To your question, the individual members will be braced at the 1 meter intervals and, this would be relative bracing. There are different formulae that account for the bracing of a column using each type of brace. These differ in that nodal bracing provides rigid brace points that do not move, while relative bracing only ensures that two brace points do not move relative to each other. In the US, AISC differentiates between nodal bracing and relative bracing. Bracing is external to the member as a whole. The lacing bars are an efficient alternative to providing solid cover plates to create a built-up member.

Lacing is not considered external bracing. AISC and AASHTO have limits on the spacing of the lacing connections based on the buckling of the compression flange of the member between lacing points.Īssuming that the lacing is designed as required, the built-up member will act like one section and the individual components do not need to be analyzed individually. In the US, codes require the lacing to be designed for about 2% of the axial load in the build-up member. The bracing must be designed so that it can transfer shear from one member to the other. For an individual member, the lacing effectively braces it at each location. The lacing is there to tie the members together to make them act as one. In laced members, the lacing is the smaller bars that go between the main members. The distance between braces on the built-up member is what matters for a given section. Individual codes might use different equations or methods to check for LTB, but the basic mechanics are the same. The controlling properties are now the combined section properties instead of the individual properties. The lacing of two members together effectively makes the built-up member act as a whole. Buckling is controlled for LTB of a beam the same way that it is controlled in a column. The rest of this answer does have some portions that would be applicable to both columns (struts) and beams though.Īs mentioned in the question, LTB occurs when the compression flange of a beam starts to rotate out of plane (buckle). This means that LTB is not a controlling consideration for the struts as pictures. They are holding the walls of the excavation apart. They are struts that are loaded primarily axially. The members in the second image are not beams.

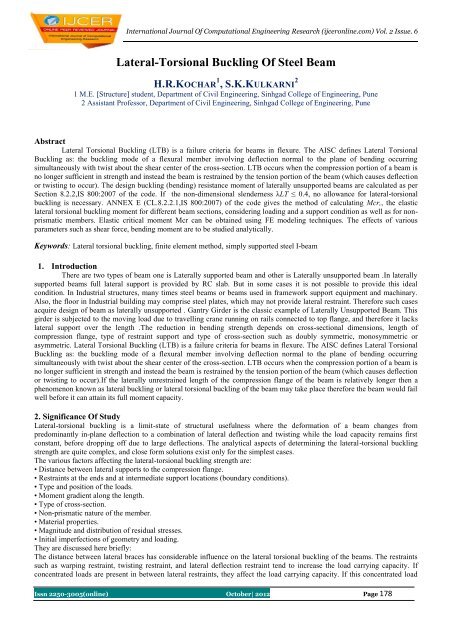
Beams are members that are loaded so that they have moment. If a 20m strut has lacings spaced at 1m intervals, what would be the effective length used to calculate LTB for the individual beam component and why?įirst off, Lateral Torsional Buckling (LTB) is only applicable to beams. However, the same could not be said of the individual beam component that made up the strut. Globally, a laced strut is not susceptible to LTB as its section modulus in the lateral direction is greater than that in the vertical direction. This is phenomenon known as lateral torsional buckling ( LTB).Ī laced strut is a built-up strut made of two (or sometimes three equally spaced) beams joined together by a system of diagonal lacings. The bottom (tension) flange restrains such movement, causing the beam to twist. But if there is enough compression with no lateral support, the flange and web would start to buckle horizontally together. The top (compression) flange would tend to buckle vertically much like a column, however, the web prevents such buckling from taking place. When loaded vertically, a beam experiences compression in its top flange and tension in its bottom flange.
